- 首頁
- 設計指南
- 3D列印圖面規範與設計指南
- 為增材製造而設計:DfAM(Design for Additive Manufacturing)金屬3D列印設計重點-擺放角度
為增材製造而設計:DfAM(Design for Additive Manufacturing)金屬3D列印設計重點-擺放角度
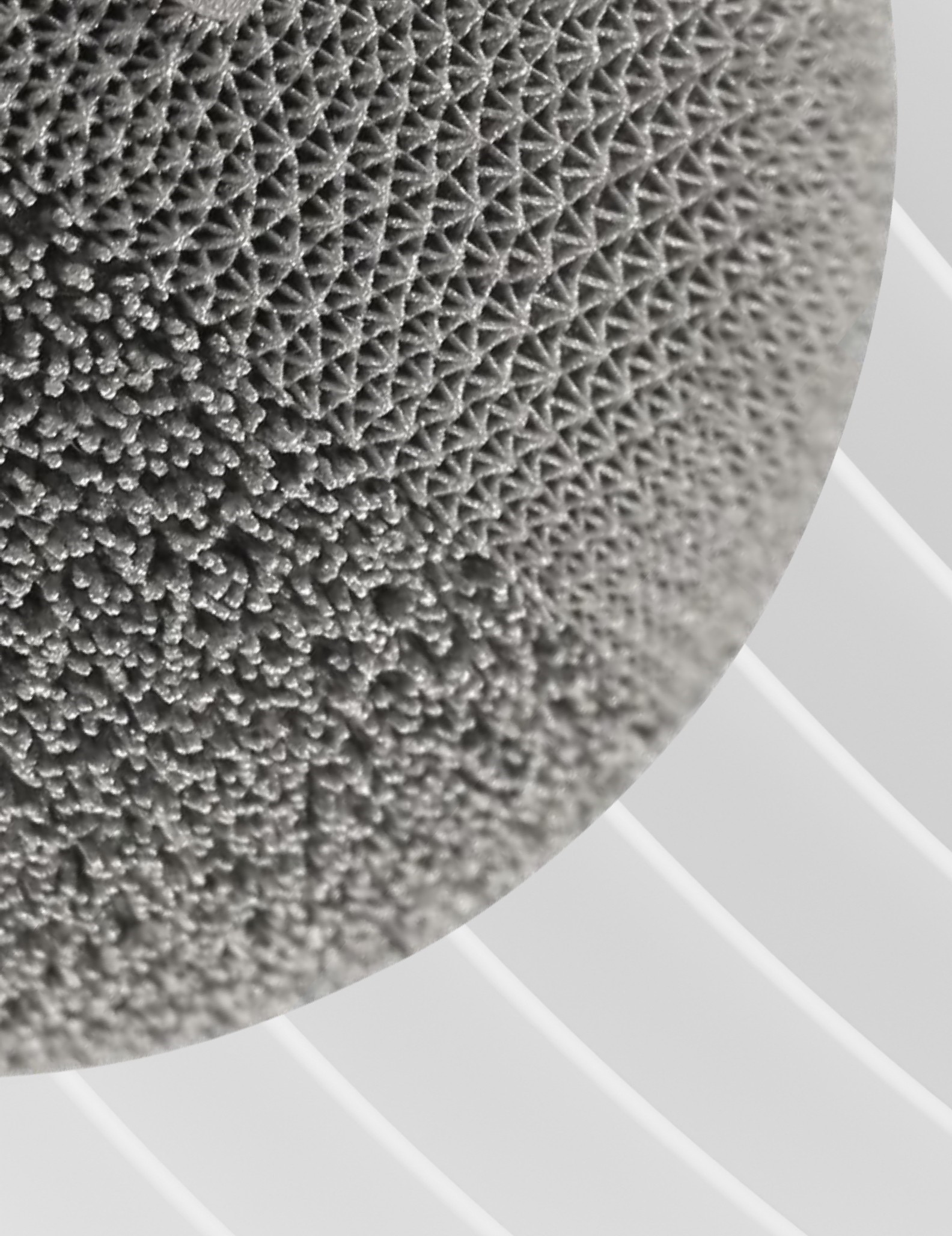
在開始增材製造的設計之前,我們先進行一番輕鬆的交談,這樣做是為了避免直接進入技術性的深奧討論,給大家一個溫暖的開場。隨後我們將討論的重點轉向了增材製造在生產過程中可能帶來的革新視角,目的是為了更有效地生產,賦予產品更多的功能性特徵,這是針對增材製造設計過程中需要考慮的關鍵點。
當我們討論增材製造技術特點時,我們特別關注於零件的放置策略。正所謂「千里之行,始於足下」,增材製造從零件的放置開始。放置方式影響了特徵結構的角度、支撐結構的設計,以及對結構的尺寸、性能的影響。討論零件放置對製造過程和最終性能的影響,其中設計對技術細節或整體質量的影響是討論的核心內容。此外,我們還將介紹增材製造中處理某些特殊結構特徵的方法。
〈延伸閱讀:金屬3D列印怎麼做? 製程關鍵因素一次帶你看!〉
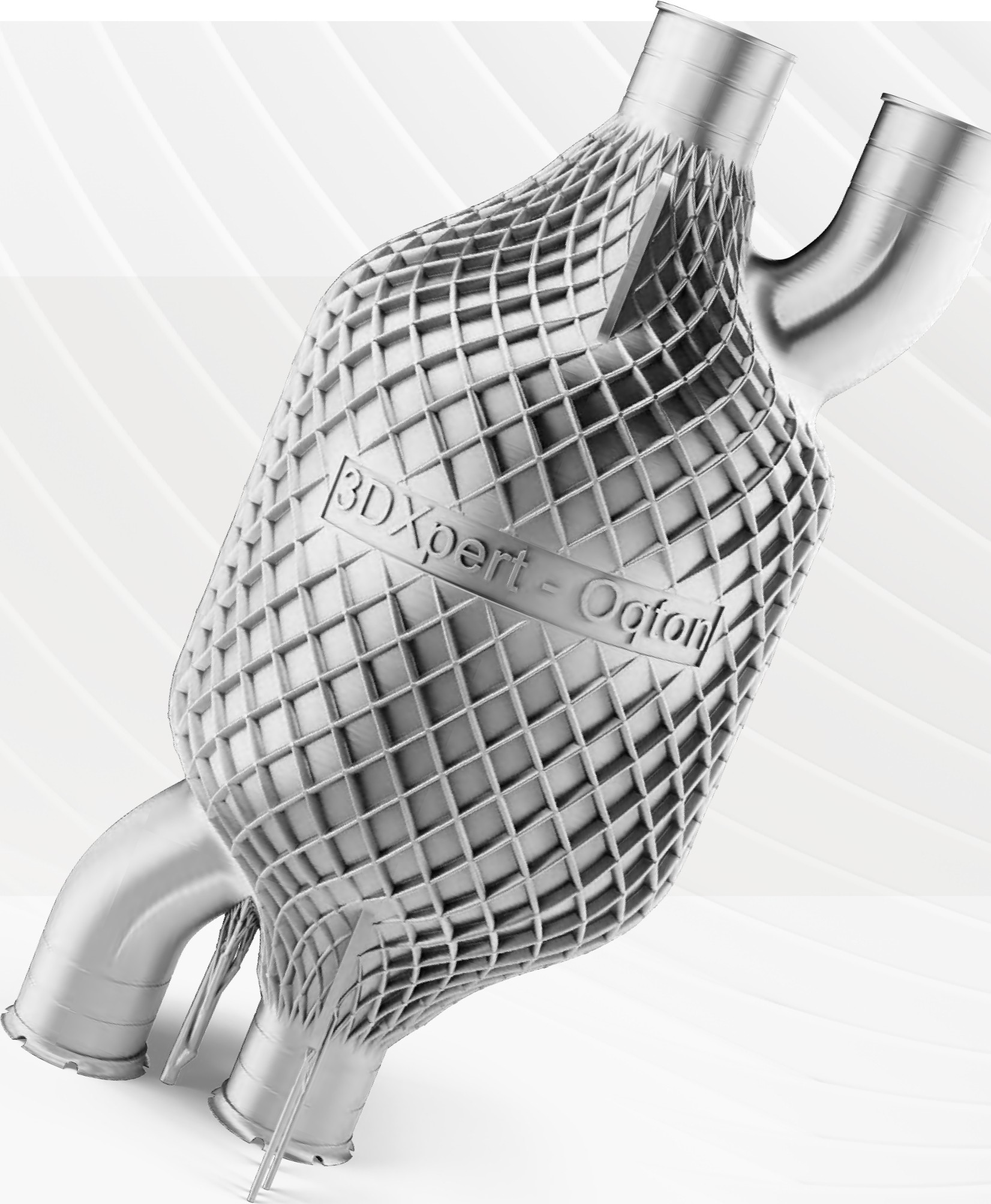
DfAM - 為增材製造而設計
「不以規矩,不成方圓。」在金屬3D列印中,若忽略支撐角度、擺放方向與結構穩定性,往往會導致列印失敗或成品質量不良。DfAM(Design for Additive Manufacturing,為增材製造而設計)是一套專為增材製造所制定的設計原則,經過眾多先驅深入研究與實務驗證。本章將針對其中幾項關鍵原則進行說明,協助設計者在實務中靈活應用,進而簡化製程、減少後處理工序,提升整體生產效率與品質。
最佳的設計不僅要考慮視覺美學,還要賦予零件額外的功能性設計,例如晶格結構、拓撲優化、隨形設計、一體化設計等。設計是靈魂所在,在這一系列賦能過程中,清晰地展現出它的重要性。如何更好地理解這些設計方法,以及如何將它們應用到零件中,接下來的章節將圍繞這些主題進行討論。
「百煉才能成鋼」,設計需要進行多次迭代,增材製造仿真在這一過程中也發揮了輔助作用。在最終生產的階段,3D列印印策略、3D列印參數以及對最終零件的成型性和質量有著重要的影響。
〈延伸閱讀:什麼是金屬3D列印模具?金屬3D列印技術的優勢與案例分析〉
DfAM設計重點:從支撐角度看零件最佳擺放策略
2c. 考慮支撐添加量:在增材製造中,從需要添加支撐的量來考慮,常常給出一個約45°斜角擺放的建議。這是因為在某些角度下,零件需要的支撐量最少,主要目的是為了避免後期移除支撐時的問題以及在金屬3D列印過程中能夠節省時間和成本。
2d. 內部支撐添加角度:從內部支撐添加的角度來看,許多時候這個選擇比較複雜,因為內部支撐難以移除或者無法移除。在擺放零件時,很多精力會花在尋找一個內部支撐較少的角度上。
2e. 金屬3D列印時的成本考量:從金屬3D列印時的成本考慮,這一頁的詳細討論將在後續的主題中展開。
2f. 綜合考慮不同因素:綜合上述不同因素,需要得出一個綜合考慮角度和內部支撐的最佳擺放角度。這樣的擺放結果和考量將在確定角度時詳細考慮。
當我們實際考察增材製造過程中零件的定位方式時,可以發現零件的放置角度對於其金屬3D列印效果和質量有著重大影響。不同的放置方式,如豎放、橫放、或斜放,對零件的性能和金屬3D列印效率會產生不同的影響:
-
豎着金屬3D列印:在這種方式下,零件的XY平面截面很小,因此承受的壓力不特別大。但是,零件放置得越高,金屬3D列印所需的時間就越長,且金屬3D列印過程中出錯的概率也會相應提高。
-
橫着金屬3D列印:當零件在XY平面上橫放時,其橫截面會變大,從而承受的壓力也會顯著增加,這可能導致零件容易發生翹曲現象。
-
斜着金屬3D列印:斜放的零件會出現階梯紋理,這是因為層厚和金屬3D列印角度導致部分切片細節丟失。
最佳的零件定位考慮了不同因素的綜合影響,給出一個綜合考慮的擺放建議。如節點2f所述,考慮的因素包括內部支撐的重要性、支撐和時間的次要考慮,而金屬3D列印時的空間範圍不作為主要考量。隨着這些擺放因素重要性的變化,最佳的零件定位也可能需要進行調整,這一點在後續的如圏4所示將進一步展開。
理想中,擺放零件時需要綜合考慮多個因素,以確定最佳的擺放方案。在實際操作過程中,通常會優先考慮某些關鍵因素,例如內部支撐的需求,然後根據這些初步的擺放結果,再根據其他因素進行調整。這種方法反映了在確定最佳擺放位置時各因素重要性的權衡。一個典型的實務操作流程是,工程師在獲得零件後,首先檢查零件哪些部位添加的支撐難以移除,在避開這些角度後,形成一個大概的擺放方向,隨後考慮支撐的數量、刮刀方向、金屬3D列印時間等因素,最終確定擺放角度。
〈延伸閱讀:一篇帶你讀懂! 從3D掃描到列印,深入探索3D列印建模的全過程!〉
零件的擺放是增材製造數據準備階段首先遇到的問題。在進行擺放時,不僅要考慮如何添加支撐,避免與刮刀碰撞,還要關注對表面金屬3D列印效果的影響。顯然,擺放對於金屬3D列印的數量、時間等也有所影響。這就是為什麼在增材製造設計初期,我們需要先討論擺放問題。
在考慮擺放時,需要關注零件的不同特徵,其中零件相對於金屬3D列印平台的角度是一個重要的考量因素。以立體零件為例,可以將零件表面根據功能和形態劃分為不同的區域,並用不同的顏色表示:
- 淺藍色表示上表面區域。
- 黃色表示下表面區域。
- 紅色表示側垂面區域。
- 粉色表示階梯面區域。
- 灰色表示垂直壁面區域。
這種顏色劃分有助於在設計和準備階段更好地視覺化和理解零件的不同面向和相關的擺放需求,進而制定出更加合理和優化的增材製造方案。
這種劃分揭示了零件的不同特徵區域,顯示出一些區域之間存在重疊,例如階梯區域既可以出現在上表面,也可能出現在下表面;部分下表面區域還可能包含側垂區域等。這樣的不同區域劃分是基於其與水平面的相對角度進行的判斷。具體到圖6中的詳細解釋,零件被藍線和紅線所圍繞的區域,其中紅線代表了某一特徵區域,該區域朝下,表示為下表面區域。上方的藍線與水平面大致平行,紅線與藍線形成一個夾角�a。根據實際情況,不同區域的劃分界限角度可以進行調整,如果按照圖6b的設置,則:
-
夾角a小於20°:這樣的區域被劃分為下表面區域,通常會產生階梯效果,需要添加支撐以保證金屬3D列印時的穩定性和精確度。這些區域以粉色表示,指出這些區域在打印過程中的特別處理需求。
-
夾角a在20°到45°之間:這些區域通常需要添加支撐,以防止金屬3D列印過程中的結構失穩或是質量問題。這些區域以紅色表示,標示出需要特別注意支撐問題的特徵區域。
-
夾角a在45°到60°之間:這些區域的處理需要根據零件結構、使用的材料以及補粉角度等因素綜合考慮,以決定是否需要添加支撐。以黃色表示,這顯示了這些區域在設計和金屬3D列印過程中可能需要更加靈活的處理方式。
-
夾角a大於60°:這些區域通常不需要添加支撐,因為夾角較大,零件的這些部分能夠在無需額外支撐的情況下穩定金屬3D列印。這些區域以灰色表示,指示出這些區域在金屬3D列印過程中相對較為簡單處理。
這種對零件特徵區域的細分和顏色標示,不僅有助於設計階段對零件進行詳細分析,也便於在金屬3D列印準備過程中針對不同區域採取適當的支撐策略,從而提高金屬3D列印效率和零件質量。
在增材製造過程中,添加支撐的一個關鍵參數是垂直角度,亦即自支撐角度。通常情況下,這個角度被設定為45°。然而,在實際應用中,這一角度可能會因材料、刮刀方向、層厚度、以及預熱溫度的不同而有所調整。對於設計師來說,在進行零件設計時,必須綜合考慮零件的朝向、垂直角度以及階梯效果角度。一旦確定了零件的最佳擺放方式,就可以進行針對性的設計優化,例如:
-
面對具有特定角度的結構:應儘量避免角度小於45°的設計,以減少需要添加支撐的情況。這裡的基本原則涵蓋了空間(如圖9a所示)、角度(如圖9b所示)以及水平孔洞(如圖9c所示),這些示意圖清晰地指出了哪些情況下需要加入支撐。
-
減少低於20°的角度設計:以避免產生階梯效應,這樣的設計原則有助於提高零件的表面質量,並減少後續的加工處理。
結構的優化不僅涉及減少必要的支撐結構,還包括對零件形狀和內部結構的細微調整,以適應金屬3D打印的特性。這包括但不限於利用倒角、調整孔徑、以及改變結構截面,以減輕打印過程中的應力集中和材料收縮對終產品質量的影響。
結論
隨著增材製造技術的不斷進步和成熟,對於設計師和工程師來說,了解和應用這些優化策略將越來越重要。這不僅能夠提升設計的實現可能性,還能夠確保製造過程的高效與經濟性,同時滿足日益嚴格的性能要求。透過持續的學習和創新,我們可以不斷推進金屬3D打印技術的發展,拓展其在各行各業的應用前景。若您對金屬3D列印有需求或疑問,都歡迎聯絡我們,探索如何透過我們的技術提升您的產品競爭力。
〈延伸閱讀:3D列印廠商怎麼選?4大3D列印廠商挑選重點〉